Industrial robotic arms work similarly to human arms. This means that the activities that a human arm can do can as well be done by a robot arm. The difference here is that a robot arm is a machine while a human arm is on a human being.
4 Advantages of Industrial Robotic Arms in Manufacturing Industries
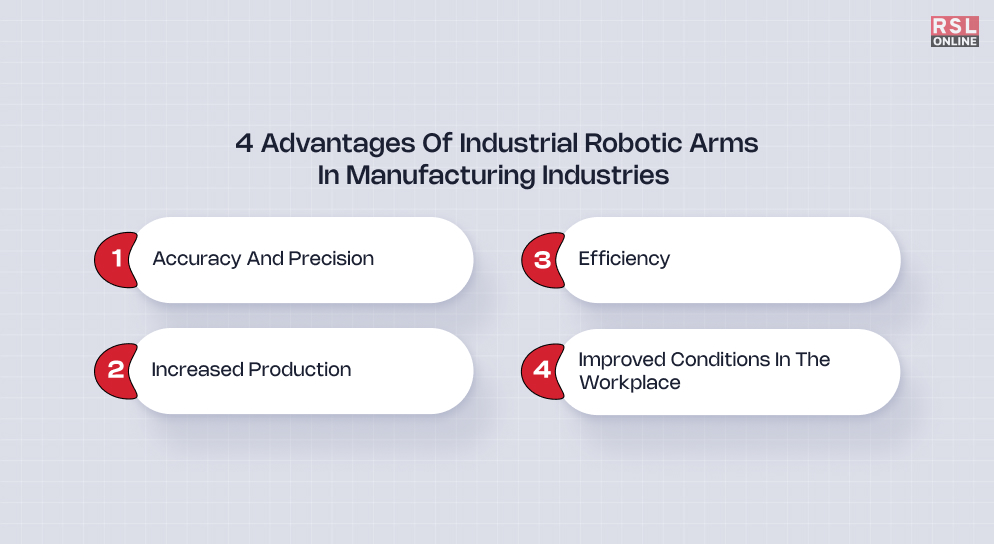
There are differences between using a industrial robotic arms and using human arms. The robot arm, however, has greater advantages than the human arm. This article will highlight four advantages of robot arms in manufacturing industries.
1. Accuracy And Precision
The robot arm, being a machine, is accurate and works as instructed. Experts operate industrial robotic arms and understand how they are run. This means that the expert in charge of a robot arm will give instructions to it and then monitor how it works. As opposed to human arms, robot arms will hardly make mistakes.
Human arms are on human beings who tend to tire and cannot work for long hours. This means that human beings need time to rest often or take breaks in between their work schedules. These breaks cater to their washroom break, time to eat, and rest, as well.
Human beings also cannot work for long hours compared to robot arms because they need time off from work. You do not get this with the robot arms that can work for a 24/7 period. Industrial robotic arms do not tire or need breaks.
All they need is instructions to run. The experts in charge of the robot arms are human beings, and they can monitor the robot arms remotely. This means that when the working hours of manufacturing industries are over, the experts do not have to remain in the location of the industry.
With the advancement of technology, manufacturing industries can purchase monitors that will enable these experts to see how the robot arms are running. In cases where the robot arms may fail, experts can rectify the fault remotely.
2. Increased Production
Human beings tire and will need breaks in between their working schedules. The time that they stop working and go out to eat or rest is the time that the manufacturing industries could use to manufacture products.
This, however, cannot be changed because human beings have to get tired. In most cases where manufacturing industries need to keep their work running, they have shifted to their manual laborers.
Henceforth, when some of their laborers go home, others come in. However, with the use of robot arms, manufacturing industries can keep their production running at all times. This means that during the day and night, the robot arms will keep following the instructions they have received.
This consequently means that the manufacturing industries will have increased production.
The use of robot arms will hence set apart the manufacturing industry from its competitors in that the people who buy from them will be assured of a continuous supply of the goods.
These goods will also be of high quality because the industrial robotic arms produce goods of the same size and shape. Organizations, business entities, and manufacturing industries that do not have the robot arm should strive to purchase one because it will give them a competitive advantage.
3. Efficiency
Robot arms also have the advantage of increasing the efficiency of manufacturing industries. The robot arms produce goods at a fast rate because they do not tire. As long as the robot arms are fed with the right instructions, they will do the tasks they ought to do in the right way.
4. Improved Conditions In The Workplace
Manufacturing Industries that make use of industrial robotic arms will often have clean surfaces. This is because they do not require any manual laborers to keep moving around them. This is opposed to when human beings work in a manufacturing industry.
Human beings have to keep moving around, and hence, their footsteps will mess up the working space. Human beings are also tired, and this comes with sweat oozing out of their skin. When manual laborers get injuries, blood may spout out, and this may spill on the surfaces of the manufacturing industries, hence dirtying the working area.
Applications Of Industrial Robotic Arms
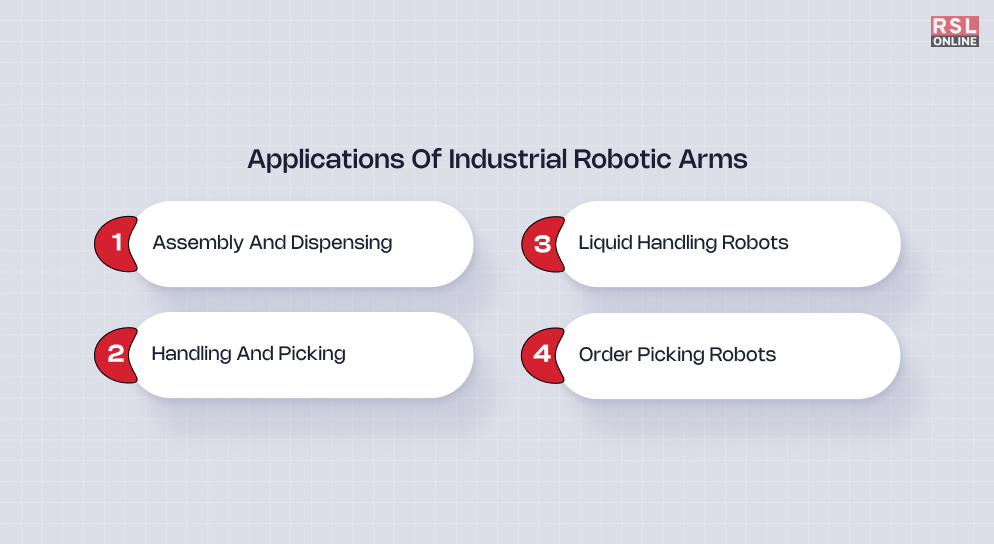
As we head towards wrapping up the discussion, let us try to understand some of the best applications of industrial robotic arms.
Assembly And Dispensing
One of the most critical steps in the manufacturing process is assembling the tiny pieces into the bigger ones. Until recently, only eyesight and human dexterity could perform these tasks.
However, with the advent of robots, the functioning of robots has attained a complete paradigm shift.
Also, robots are great in administering the bonding chemicals in the related technology. Yes, adhesive and sealants are used. These tasks include fasting to join components.
Handling And Picking
You may have seen the use of large cran robots drawing in the manufacturing and warehousing industry. Forklifts are used to operate autonomously. It brings down human labor significantly.
There are the smaller carts, which are known as Autonomous mobile robots. (AMRs). The companies frequently use these industrial robotic arms to move the packaged stations. Moreover, transporting things inside the building has been accomplished traditionally using a conveyor system.
Liquid Handling Robots
Another great example of industrial robotic arms is the application of frequent pipetting. It includes testing, medical samples, and examining the chemical makeup of liquids. They are also used in conducting biological experiments.
A small amount of liquid is drawn into a syringe and is measured precisely as the amount that must be transferred from one place to another. Pipetting, when managed by humans, was labor intensive.
However, the scenario has changed drastically since the advent of industrial robotic arms.
Order Picking Robots: Excellent Use Of Industrial Robotic Arms
Order-picking management with industrial robot arms has brought in a huge change. These highly developed robots have become accessible in recent times.
Moreover, the incredible range of things that robots encounter is one of the reasons behind building these extremely helpful robotic devices. Transporting things inside the building was implemented using conveyor systems that employ revolving cylinders. However, with new technology integrations, the entire activity has gained pace.
Other than this, stakeholders are using industrial robotic arms for machine tending, loading, and even cutting. There, you have milling robots, drilling robots, and laser-cutting robots that are doing their tasks with the utmost dexterity.
As much as robot arms may do away with human beings in the workplace, they come with great advantages.
Additional Reading: