Preventative maintenance regularly services machinery to avoid malfunctions and downtime.
Whether you’re managing a manufacturing plant or a tech company, maintaining the health of your equipment is paramount. Efficiency, equipment lifespan, and financial resources can be improved through early detection and prevention of small defects.
Planning a robust preventive maintenance schedule involves understanding your equipment’s functionality, maintenance requirements, and lifecycle. With a well-structured plan and efficient scheduling, you can ensure your equipment remains reliable, safe, and long-lasting.
This article will delve into the key strategies for optimal planning of a preventive maintenance schedule, offering insights into creating a smooth and efficient operation.
The Importance Of Maintenance Management
Maintenance management stands at the crossroads between efficient operations and the longevity of your equipment. You can improve productivity and extend equipment lifespan by effectively coordinating tasks, allocating resources, maintaining an inventory, and minimizing downtime.
Let’s delve into these key aspects:
- Coordinating Maintenance Activities: It involves orchestrating various maintenance tasks to ensure smooth operations. For example, in a factory, maintenance teams may need to work in shifts to cover machinery inspection around the clock.
- Efficiently Allocating Resources: Resource allocation involves assigning the right personnel, tools, and time to each maintenance task. For instance, if a complex piece of equipment needs repair, a highly skilled technician should be assigned rather than a junior employee.
- Maintaining an Inventory of Spare Parts: Having spare parts on hand can reduce downtime when equipment failures occur. For example, keeping extra conveyor belts in stock in a packaging plant can prevent long delays if a belt wears out.
- Ensuring Minimal Downtime: Maintenance management minimizes equipment downtime for repairs. This might involve scheduling maintenance during off-peak hours or having contingency plans for quick repairs.
Effective maintenance management is a proactive approach that mitigates the risk of sudden equipment failure and helps ensure consistent productivity.
Components Of A Robust Preventive Maintenance Plan
Preventive maintenance requires numerous key elements. These elements form a blueprint that guides your maintenance strategy and shapes the trajectory of your equipment’s lifespan.
Let’s explore these components:
- Maintenance of Equipment: This process involves conducting regular inspections and minor repairs to prevent major equipment failures. Regular dough mixer lubrication in a bakery can avoid wear and tear and prevent loss during peak production hours.
- Plant Maintenance: Beyond individual pieces of equipment, preventive maintenance extends to the infrastructure and environment housing the equipment. Proper maintenance of these elements can have a direct impact on equipment performance. For example, maintaining optimal ventilation in a data center can help prevent overheating and prolong the life of servers.
- Planning and Scheduling: The success of preventive maintenance hinges on meticulous planning and scheduling. Detailed plans and schedules ensure regular maintenance, reducing the chances of unexpected equipment failure. A warehouse might, for instance, schedule a forklift for a bi-annual inspection to ensure it remains in good working condition.
- Equipment Reliability: Assessing the condition and performance of equipment over time is a crucial part of preventive maintenance. Regular checks can provide insights that help predict and prevent equipment failures. A company could monitor its industrial printer’s performance to identify decreased efficiency patterns, indicating the need for maintenance before a major malfunction occurs.
Understanding these components is instrumental in crafting a robust preventive maintenance plan that ensures equipment longevity and operational efficiency.
Strategies For Planning And Scheduling Preventive Maintenance
Effective planning and scheduling form the bedrock of a successful preventive maintenance program. Thoughtful strategies can maximize equipment uptime, minimize unexpected failures, and reduce maintenance costs.
Let’s consider some key strategies:
- Understanding Your Equipment: Deep familiarity with each equipment’s functioning, maintenance requirements, and lifecycle is essential. For example, a conveyor belt system used constantly throughout the day in a retail warehouse may require weekly inspections to ensure optimal function. On the other hand, a backup generator used infrequently might only need a monthly check-up.
- Incorporating Equipment Reliability into the Schedule: Equipment reliability should inform your maintenance schedule. Highly reliable equipment, such as a state-of-the-art CNC machine with a robust build and proven track record, may need less frequent preventive checks. Conversely, older or less reliable equipment, like a vintage lathe machine, may demand more regular attention to avoid unexpected breakdowns.
- Utilizing a Maintenance Management System: Leveraging technology can streamline planning and scheduling. Maintenance management software, such as a computerized maintenance management system (CMMS), can help track maintenance activities and generate alerts for upcoming maintenance tasks. For instance, a CMMS might send a notification when it’s time for the quarterly maintenance of an HVAC system, helping to ensure this important task isn’t overlooked.
These ideas can assist in building a successful and efficient preventative maintenance schedule, improving operations and equipment life.
Conducting A Reliability Assessment
A reliability assessment is a barometer for your equipment’s performance and dependability. This comprehensive review can offer valuable insights into the health of your machines, enabling more informed maintenance planning. It aids to:
- Identify Equipment with High Failure Rates: A reliability assessment helps pinpoint problematic equipment that frequently breaks down. For example, a packaging machine that halts production due to frequent jams could be identified for more targeted maintenance.
- Predict Potential Failures: You can forecast potential issues by analyzing equipment performance data. For instance, a motor showing gradually increasing temperature trends may be heading toward an overheating problem.
- Plan Preventive Maintenance Accordingly: You can adjust your preventive maintenance schedule based on the insights gained. For example, if an assessment reveals a particular HVAC unit tends to malfunction every six months, a preventative maintenance session could be scheduled every four months to pre-empt potential breakdowns.
The Role of Maintenance on Equipment and Plant Maintenance in Preventive Maintenance
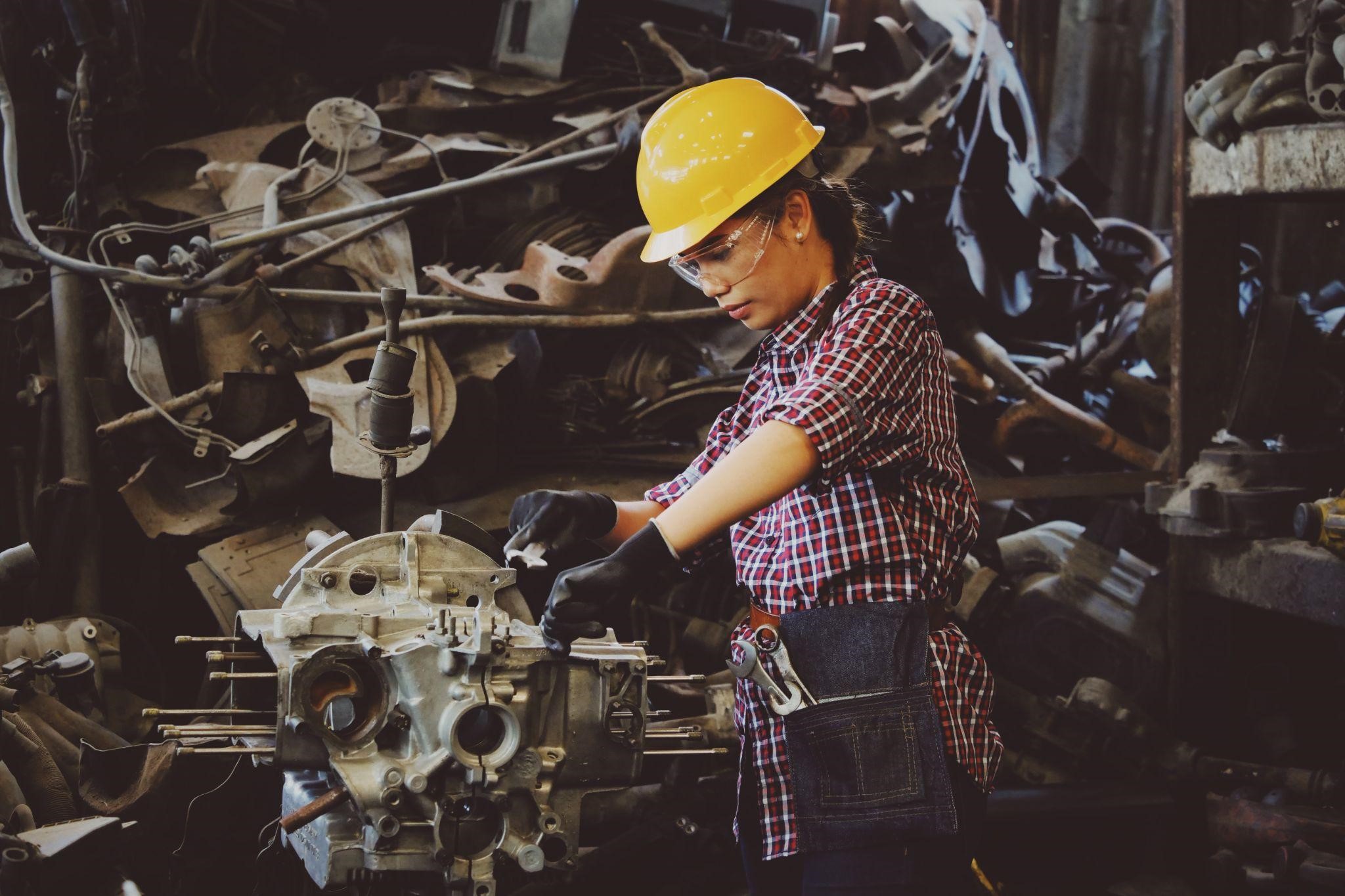
Maintenance of individual equipment and overall plant maintenance form the two pillars supporting a robust preventive maintenance strategy:
- Maintenance of Equipment: Regular checks can uncover minor issues before they snowball into major problems. For example, frequently changing the filters on an industrial vacuum cleaner can prevent dust accumulation, ensuring optimal suction power and preventing motor damage.
- Plant Maintenance: A well-maintained plant environment can significantly enhance equipment performance. For instance, in a metalworking shop, controlling humidity can prevent rusting and wear of the machinery, thereby prolonging equipment lifespan and ensuring better performance.
The Impact Of Efficient Planning And Scheduling On Equipment Reliability
Efficient planning and scheduling are the cornerstones that bolster equipment reliability, playing several crucial roles:
- Regular Maintenance: Ensuring equipment is serviced at appropriate intervals can significantly prolong its lifespan. For example, scheduling frequent oil changes for a company’s fleet of trucks can prevent engine wear and extend the vehicles’ operational life.
- Predictive Maintenance: Regular checks and data analysis can help identify issues before they cause equipment failure. For example, noticing an unusual increase in the noise level from a pump might suggest a bearing issue that can be fixed before it results in a costly breakdown.
- Minimized Downtime: Swift and effective maintenance reduces the occurrence of unexpected breakdowns, leading to increased operational time. This might involve maintaining a well-stocked spare parts inventory to ensure quick replacements and repairs and keeping machinery up and running.
Understanding and implementing these factors can significantly impact your preventive maintenance program, improving equipment reliability and operational efficiency.
Final Thoughts
In summary, preventive maintenance is vital to any organization relying on machinery. It ensures that potential failures are detected and resolved promptly, which leads to increased equipment reliability and decreased downtime.
Following the outlined strategies for optimal planning and scheduling can go a long way in improving the effectiveness of your preventive maintenance plan.
Read Also: